Tripleks is makke fan trije of mear tinne lagen hout dy't mei in lijm oaninoar ferbûn binne. Elke laach hout, of tripleks, wurdt meastentiids sa oriïntearre dat de nerven yn in rjochte hoeke rinne mei de oanbuorjende laach om de krimp te ferminderjen en de sterkte fan it ôfmakke stik te ferbetterjen. It measte tripleks wurdt parse ta grutte, platte platen dy't brûkt wurde yn boukonstruksje. Oare stikken tripleks kinne foarme wurde ta ienfâldige of gearstalde krommingen foar gebrûk yn meubels, boaten en fleantugen.
It gebrûk fan tinne lagen hout as konstruksjemiddel datearret út sawat 1500 f.Kr. doe't Egyptyske ambachtslju tinne stikken donker ebbenhout oan 'e bûtenkant fan in sederkiste ferbûnen dy't fûn waard yn it grêf fan kening Tut-Ankh-Amon. Dizze technyk waard letter brûkt troch de Griken en Romeinen om moaie meubels en oare dekorative objekten te produsearjen. Yn 'e 17e iuw waard de keunst fan it dekorearjen fan meubels mei tinne stikken hout bekend as fineerwurk, en de stikken sels waarden bekend as fineerwurk.
Oant de lette 1700's waarden de stikken fineer folslein mei de hân snien. Yn 1797 frege de Ingelsman Sir Samuel Bentham patinten oan foar ferskate masines om fineers te produsearjen. Yn syn patintoanfragen beskreau hy it konsept fan it laminearjen fan ferskate lagen fineer mei lym om in dikker stik te foarmjen - de earste beskriuwing fan wat wy no tripleks neame.
Nettsjinsteande dizze ûntwikkeling duorre it hast noch hûndert jier foardat laminearre fineer kommersjele gebrûken fûn bûten de meubelyndustry. Om 1890 hinne waarden laminearre hout foar it earst brûkt om doarren te bouwen. Doe't de fraach groeide, begûnen ferskate bedriuwen mei it produsearjen fan platen fan mearlaachs laminearre hout, net allinich foar doarren, mar ek foar gebrûk yn spoarweinen, bussen en fleantugen. Nettsjinsteande dit tanommen gebrûk soarge it konsept fan it brûken fan "plakt hout", sa't guon ambachtslju it sarkastysk neamden, foar in negatyf byld foar it produkt. Om dit byld tsjin te gean, kamen de fabrikanten fan laminearre hout byinoar en kamen úteinlik ta de term "multipleks" om it nije materiaal te beskriuwen.
Yn 1928 waarden de earste standertgrutte tripleksplaten fan 1,2 by 2,4 m (4 ft by 8 ft) yn 'e Feriene Steaten yntrodusearre foar gebrûk as algemien boumateriaal. Yn 'e folgjende desennia makken ferbettere lijmen en nije produksjemetoaden it mooglik om tripleks te brûken foar in breed ferskaat oan tapassingen. Tsjintwurdich hat tripleks snien hout ferfongen foar in protte boudoelen, en is de produksje fan tripleks in wrâldwide yndustry fan meardere miljarden dollars wurden.
De bûtenste lagen fan tripleks binne respektivelik bekend as de foarkant en de efterkant. De foarkant is it oerflak dat brûkt of sjoen wurde moat, wylst de efterkant net brûkt of ferburgen bliuwt. De middelste laach is bekend as de kearn. Yn tripleks mei fiif of mear lagen binne de tuskenlagen bekend as de krúsbannen.
Tripleks kin makke wurde fan hurdhout, sêfthout, of in kombinaasje fan 'e twa. Guon gewoane hurdhouten binne jiske, maple, mahonie, ike en teak. It meast foarkommende sêfthout dat brûkt wurdt om tripleks te meitsjen yn 'e Feriene Steaten is Douglas-spar, hoewol ferskate soarten pine, seder, spar en redwood ek brûkt wurde.
Komposit tripleks hat in kearn makke fan spaanplaat of stikken hout dy't fan râne oan râne ferbûn binne. It is ôfmakke mei in foar- en efterkant fan tripleksfineer. Komposit tripleks wurdt brûkt wêr't tige dikke platen nedich binne.
It type lijm dat brûkt wurdt om de lagen hout oan elkoar te binen hinget ôf fan 'e spesifike tapassing foar it ôfmakke tripleks. Sêfthouten tripleksplaten ûntworpen foar ynstallaasje oan 'e bûtenkant fan in struktuer brûke meastentiids in fenol-formaldehydehars as lijm fanwegen syn poerbêste sterkte en wjerstân tsjin focht. Sêfthouten tripleksplaten ûntworpen foar ynstallaasje oan 'e binnenkant fan in struktuer kinne in bloedproteïne- of in soja-proteïnelijm brûke, hoewol de measte sêfthouten ynterieurplaten no makke binne mei deselde fenol-formaldehydehars dy't brûkt wurdt foar bûtenplaten. Hardhouten tripleks dat brûkt wurdt foar ynterieur tapassingen en by de konstruksje fan meubels wurdt meastentiids makke mei in ureum-formaldehydehars.
Guon tapassingen fereaskje tripleksplaten mei in tinne laach plestik, metaal, of mei hars ympregnearre papier of stof dy't oan 'e foarkant of efterkant (of beide) ferbûn is om it bûtenste oerflak ekstra wjerstân te jaan tsjin focht en skuring of om de ferve-hâldende eigenskippen te ferbetterjen. Sok tripleks wurdt oerlaad tripleks neamd en wurdt faak brûkt yn 'e bou, ferfier en lânbou-yndustry.
Oare tripleksplaten kinne wurde bedekt mei in floeibere beits om de oerflakken in ôfmakke uterlik te jaan, of kinne wurde behannele mei ferskate gemikaliën om de flamresistinsje of ferset tsjin ferfal fan it tripleks te ferbetterjen.
Der binne twa brede klassen fan tripleks, elk mei in eigen gradearringssysteem.
Ien klasse is bekend as bou en yndustrieel. Tripleks yn dizze klasse wurdt benammen brûkt foar har sterkte en wurdt beoardiele op har bleatstellingsfermogen en de kwaliteit fan fineer dat brûkt wurdt op 'e foar- en efterkant. De bleatstellingsfermogen kin binnen- of bûtenkant wêze, ôfhinklik fan it type lijm. Fineerkwaliteiten kinne N, A, B, C of D wêze. N-kwaliteit hat heul pear oerflakdefekten, wylst D-kwaliteit ferskate knopen en spleten kin hawwe. Bygelyks, tripleks dat brûkt wurdt foar ûnderflierren yn in hûs wurdt beoardiele as "Ynterieur CD". Dit betsjut dat it in C-foarkant hat mei in D-efterkant, en de lijm is geskikt foar gebrûk op beskerme lokaasjes. De binnenste lagen fan alle bou- en yndustrieel tripleks binne makke fan kwaliteit C- of D-fineer, nettsjinsteande de wurdearring.
De oare klasse fan tripleks is bekend as hardhout en dekoratyf. Tripleks yn dizze klasse wurdt benammen brûkt foar har uterlik en wurdt yn ôfnimmende folchoarder fan wjerstân tsjin focht klassifisearre as Technysk (Eksterieur), Type I (Eksterieur), Type II (Ynterieur) en Type III (Ynterieur). Harren frontfineer binne praktysk frij fan mankeminten.
Grutte
Tripleksplaten fariearje yn dikte fan 1,6 mm oant 76 mm. De meast foarkommende diktes binne yn it berik fan 6,4 mm oant 19,0 mm. Hoewol de kearn, de krúsbannen, en de foar- en efterkant fan in tripleksplaat makke kinne wêze fan fineer fan ferskillende dikte, moat de dikte fan elk lykwichtich wêze om it sintrum hinne. Bygelyks, de foar- en efterkant moatte fan gelikense dikte wêze. Likegoed moatte de boppeste en ûnderste krúsbannen gelyk wêze.
De meast foarkommende grutte foar tripleksplaten dy't brûkt wurde yn boukonstruksje is 4 ft (1,2 m) breed en 8 ft (2,4 m) lang. Oare gewoane breedtes binne 3 ft (0,9 m) en 5 ft (1,5 m). Lingtes fariearje fan 8 ft (2,4 m) oant 12 ft (3,6 m) yn stappen fan 1 ft (0,3 m). Spesjale tapassingen lykas boatbou kinne gruttere platen fereaskje.
De beammen dy't brûkt wurde om tripleks te meitsjen binne oer it algemien lytser yn diameter as dy brûkt om hout te meitsjen. Yn 'e measte gefallen binne se plante en groeid yn gebieten dy't eigendom binne fan it tripleksbedriuw. Dizze gebieten wurde soarchfâldich beheard om de groei fan 'e beam te maksimalisearjen en skea troch ynsekten of fjoer te minimalisearjen.
Hjir is in typyske folchoarder fan operaasjes foar it ferwurkjen fan beammen ta standert tripleksplaten fan 1,2 by 2,4 m (4 ft by 8 ft):
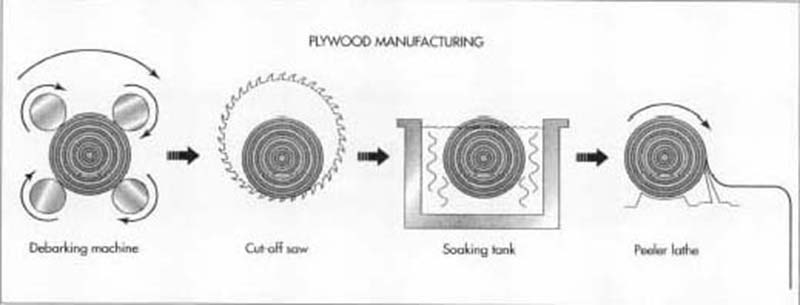
De stammen wurde earst ûntbast en dan yn skilblokken snien. Om de blokken yn strips fineer te snijen, wurde se earst wiet makke en dan yn strips skild.
1 Selektearre beammen yn in gebiet wurde markearre as klear om te wurden omkapt of omkapt. It kappen kin dien wurde mei benzine-oandreaune kettingseagen of mei grutte hydraulyske skjirre dy't oan 'e foarkant fan tsjilferfiermiddels monteard binne, dy't kappen neamd wurde. De tûken wurde mei kettingseagen fan 'e omfallen beammen fuorthelle.
2 De snoeide beamstammen, of beamstammen, wurde nei in laadplak sleept troch tsjilferfiermiddels dy't skidders neamd wurde. De beamstammen wurde op lingte snien en wurde op frachtweinen laden foar de reis nei de tripleksfabryk, dêr't se yn lange stapels steapele wurde, bekend as beamdekken.
3 As der stammen nedich binne, wurde se fan 'e stammedekken oppakt troch rubberbannenladers en op in kettingtransporteur pleatst dy't se nei de ûntbastmasine bringt. Dizze masine ferwideret de bast, mei skerptoske slypskiven of mei wetterstralen ûnder hege druk, wylst de stamme stadich om syn lange as draaid wurdt.
4 De ûntbaste stammen wurde op in kettingtransporteur de mûne ynfierd, dêr't in enoarme sirkelseage se yn seksjes snijt fan sawat 2,5 m oant 2,6 m lang, geskikt foar it meitsjen fan standert platen fan 2,4 m lang. Dizze stammeseksjes binne bekend as peelerblokken.
5 Foardat it fineer snien wurde kin, moatte de peelerblokken ferwaarme en wiet wurde om it hout sêfter te meitsjen. De blokken kinne stoomd wurde of yn hyt wetter ûnderdompele wurde. Dit proses duorret 12-40 oeren, ôfhinklik fan it type hout, de diameter fan it blok en oare faktoaren.
6 De ferwaarme skilblokken wurde dan nei de skildraaibank ferfierd, dêr't se automatysk útrjochte wurde en ien foar ien yn 'e draaibank ynfierd wurde. Wylst de draaibank it blok rap om syn lange as draait, skilt in mesblêd oer de folsleine lingte in trochgeande laach fineer fan it oerflak fan it spinblok mei in snelheid fan 90-240 m/min. As de diameter fan it blok fermindere wurdt nei sawat 230-305 mm, wurdt it oerbleaune stik hout, bekend as de skilkearn, út 'e draaibank smiten en wurdt in nij skilblok op syn plak ynfierd.
7 It lange blêd fineer dat út 'e peelerdraaibank komt, kin fuortendaliks ferwurke wurde, of it kin opslein wurde yn lange trays mei meardere nivo's of op rollen wûn wurde. Yn alle gefallen omfettet it folgjende proses it snijen fan it fineer yn brûkbere breedtes, meastal sawat 1,4 m (4 ft-6 in), foar it meitsjen fan standert tripleksplaten fan 1,2 m (4 ft). Tagelyk sykje optyske scanners nei seksjes mei ûnakseptabele defekten, en dizze wurde útknipt, wêrtroch't stikken fineer minder breed as de standert oerbliuwe.
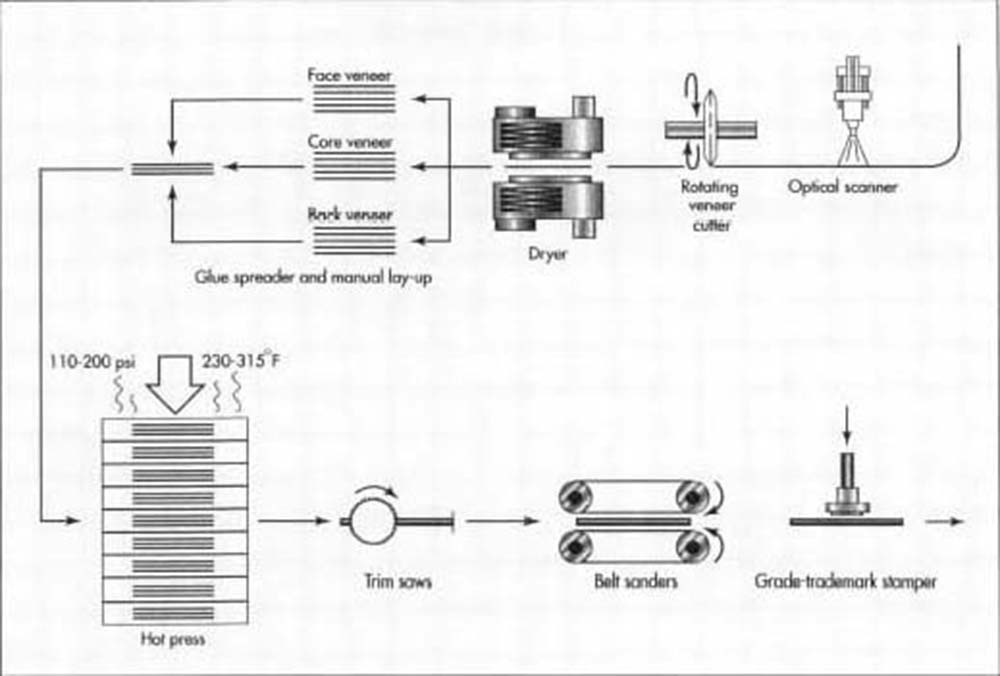
De wiete strips fineer wurde op in rol rôle, wylst in optyske scanner alle ûnakseptabele defekten yn it hout detektearret. Sadree't it droech is, wurdt it fineer sortearre en steapele. Selektearre stikken fineer wurde oaninoar lijmd. In hjitte parse wurdt brûkt om it fineer te fersegeljen ta ien fêst stik tripleks, dat knipt en skuurd wurdt foardat it mei de juste kwaliteit stempeld wurdt.
8 De stikken fineer wurde dan sortearre en steapele neffens kwaliteit. Dit kin mei de hân dien wurde, of it kin automatysk dien wurde mei optyske scanners.
9 De sortearre seksjes wurde yn in droeger fiede om har fochtgehalte te ferminderjen en se te litten krimpen foardat se oaninoar lijmd wurde. De measte tripleksfabriken brûke in meganyske droeger wêryn't de stikken kontinu troch in ferwaarme keamer bewege. Yn guon droegers wurde stralen fan hege snelheid, ferwaarme loft oer it oerflak fan 'e stikken blaasd om it droechproses te fersnellen.
10 As de seksjes fineer út 'e droeger komme, wurde se neffens kwaliteit steapele. Seksjes ûnder de breedte hawwe ekstra fineer dy't der mei tape of lym oan ferbûn binne om stikken geskikt te meitsjen foar gebrûk yn 'e ynderlike lagen dêr't uterlik en sterkte minder wichtich binne.
11 Dy stikken fineer dy't dwers oer de grins ynstalleare wurde sille - de kearn yn trijelaags platen, of de dwersbannen yn fiiflaags platen - wurde yn lingten fan sawat 1,3 m (4 ft-3 inch) snien.
12 As de passende stikken fineer gearstald binne foar in bepaalde run tripleks, begjint it proses fan it oplizzen en lijmen fan 'e stikken oaninoar. Dit kin mei de hân of healautomatysk mei masines dien wurde. Yn it ienfâldichste gefal fan trijelaags platen wurdt it efterste fineer flak lein en troch in lijmfersprieder laat, dy't in laach lijm oanbringt op it boppeste oerflak. De koarte stikken kearnfineer wurde dan dwers oer de lijmde efterkant lein, en it hiele plaat wurdt in twadde kear troch de lijmfersprieder laat. Uteinlik wurdt it foarste fineer boppe op 'e lijmde kearn lein, en it plaat wurdt steapele mei oare platen dy't wachtsje om yn 'e parse te gean.
13 De lijmde platen wurde yn in hjitte parse mei meardere iepeningen laden. Persen kinne 20-40 platen tagelyk behannelje, wêrby't elk plaat yn in aparte sleuf laden wurdt. As alle platen laden binne, perst de parse se byinoar ûnder in druk fan sawat 110-200 psi (7,6-13,8 bar), wylst se tagelyk ferwaarme wurde ta in temperatuer fan sawat 230-315° F (109,9-157,2° C). De druk soarget foar goed kontakt tusken de lagen fineer, en de waarmte soarget derfoar dat de lijm goed úthardt foar maksimale sterkte. Nei in perioade fan 2-7 minuten wurdt de parse iepene en wurde de platen derút helle.
14 De rûge platen geane dan troch in set seagen, dy't se oant har definitive breedte en lingte snije. Hegere kwaliteit platen geane troch in set fan 1,2 m brede bandskuurmasines, dy't sawol de foar- as efterkant skuurje. Platen fan tuskenlizzende kwaliteit wurde mei de hân spot-skuurd om rûge gebieten skjin te meitsjen. Guon platen wurde troch in set sirkelseageblêden laat, dy't ûndjippe groeven yn 'e foarkant snije om it tripleks in tekstuerde uterlik te jaan. Nei in lêste ynspeksje wurde alle oerbleaune defekten reparearre.
15 De ôfmakke platen wurde bestimpele mei in hannelsmerk dat de keaper ynformaasje jout oer de bleatstellingswurdearring, de kwaliteit, it fabryksnûmer en oare faktoaren. Plakken fan itselde hannelsmerk wurde yn stapels oaninoar bûn en nei it pakhús ferpleatst om te wachtsjen op ferstjoering.
Krekt as mei hout bestiet der net sa'n ding as in perfekt stik tripleks. Alle stikken tripleks hawwe in bepaald oantal defekten. It oantal en de lokaasje fan dizze defekten bepaalt de tripleksklasse. Normen foar bou- en yndustrieel tripleks wurde definieare troch Produktstandert PS1 taret troch it National Bureau of Standards en de American Plywood Association. Normen foar hardhout en dekorative tripleks wurde definieare troch ANSIIHPMA HP taret troch it American National Standards Institute en de Hardwood Plywood Manufacturers' Association. Dizze noarmen stelle net allinich de klassifikaasjesystemen foar tripleks fêst, mar spesifisearje ek konstruksje-, prestaasjes- en tapassingskritearia.
Sels hoewol tripleks beammen frij effisjint brûkt - yn essinsje wurde se útinoar helle en wer byinoar set yn in sterkere, brûkberder konfiguraasje - is der noch altyd in soad ôffal yn it produksjeproses. Yn 'e measte gefallen wurdt mar sawat 50-75% fan it brûkbere folume hout yn in beam omset yn tripleks. Om dit sifer te ferbetterjen, binne ferskate nije produkten yn ûntwikkeling.
Ien nij produkt hjit oriïntearre strandboard, dat makke wurdt troch de hiele beamstam yn triedden te fersnipperjen, ynstee fan in fineer fan 'e beamstam te pellen en de kearn fuort te smiten. De triedden wurde mingd mei in lijm en yn lagen komprimearre mei de nerven yn ien rjochting. Dizze komprimearre lagen wurde dan rjochthoekich op elkoar oriïntearre, lykas tripleks, en wurde oaninoar ferbûn. Orientearre strandboard is like sterk as tripleks en kostet wat minder.
Pleatsingstiid: 10 augustus 2021